The rapid temperature change damp heat test chamber refers to a method of screening the weather, thermal or mechanical stress that may cause premature failure of the sample. For example, it can find defects in the design of the electronic module, materials or production. Stress screening (ESS) technology can detect early failures in the development and production stages, reduce the risk of failure due to design selection errors or poor manufacturing processes, and greatly improve product reliability. Through environmental stress screening, unreliable systems that have entered the production test stage can be found. It has been used as a standard method for quality improvement to effectively extend the normal working life of the product. The SES system has automatic adjustment functions for refrigeration, heating, dehumidification, and humidification (humidity function is only for the SES system). It is mainly used for temperature stress screening. It can also be used for traditional high temperature, low temperature, high and low temperature cycles, constant humidity, heat, and humidity. Environmental tests such as damp heat, temperature and humidity combination, etc.
Features:
Temperature change rate 5℃/Min.10℃/Min.15℃/Min.20℃/Min iso-average temperature
The humidity box is designed to be non-condensing to avoid misjudgment of test results.
Programmable load power supply 4 ON/OFF output control to protect the safety of the equipment under test
Expandable APP mobile platform management. Expandable remote service functions.
Environmentally friendly refrigerant flow control, energy-saving and power-saving, fast heating and cooling rate
Independent anti-condensation function and temperature, no wind and smoke protection function of the product under test
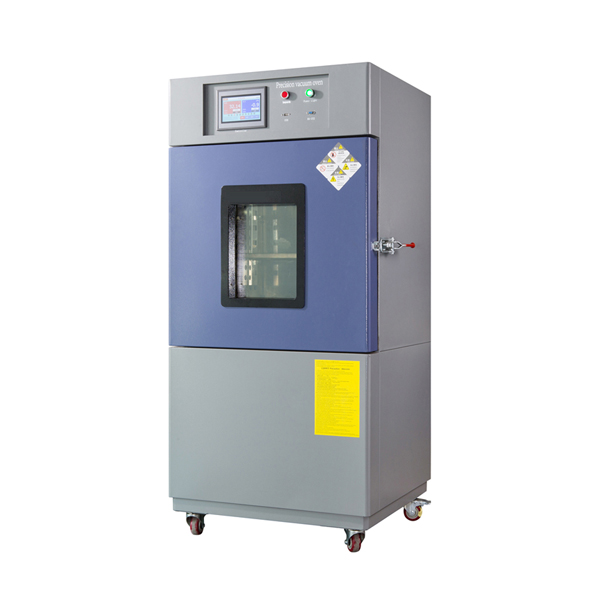
Unique operation mode, after the test, the cabinet returns to room temperature to protect the product under test
Scalable network video surveillance, synchronized with data testing
Control system maintenance automatic reminder and fault case software design function
Color screen 32-bit control system E Ethernet E management, UCB data access function
Specially designed dry air purge to protect the product under test from rapid temperature change due to surface condensation
Industry low humidity range 20℃/10% control ability
Equipped with automatic water supply system, pure water filtration system and water shortage reminder function
Meet the stress screening of electronic equipment products, lead-free process, MIL-STD-2164, MIL-344A-4-16, MIL-2164A-19, NABMAT-9492, GJB-1032-90, GJB/Z34-5.1.6, IPC -9701...and other test requirements. Note: The temperature and humidity distribution uniformity test method is based on the effective space measurement of the distance between the inner box and each side 1/10 (GB5170.18-87)
In the working process of electronic products, in addition to electrical stress such as voltage and current of electrical load, environmental stress also includes high temperature and temperature cycle, mechanical vibration and shock, humidity and salt spray, electromagnetic field interference, etc. Under the action of the above-mentioned environmental stress, the product may experience performance degradation, parameter drift, material corrosion, etc., or even failure.
After electronic products are manufactured, from screening, inventory, transportation to use, and maintenance, they are all affected by environmental stress, causing the physical, chemical, mechanical and electrical properties of the product to change continuously. The change process can be slow or Transient, it depends entirely on the type of environmental stress and the magnitude of the stress.
The steady-state temperature stress refers to the response temperature of an electronic product when it is working or stored in a certain temperature environment. When the response temperature exceeds the limit that the product can withstand, the component product will not be able to work within the specified electrical parameter range, which may cause the product material to soften and deform or reduce the insulation performance, or even burn out due to overheating. For the product, the product is exposed to high temperature at this time. Stress, high-temperature over-stress can cause product failure in a short time of action; when the response temperature does not exceed the specified operating temperature range of the product, the effect of steady-state temperature stress is manifested in the effect of long-term action. The effect of time causes the product material to gradually age, and the electrical performance parameters are drifting or poor, which eventually leads to the product failure. For the product, the temperature stress at this time is the long-term temperature stress. The steady-state temperature stress experienced by electronic products comes from the ambient temperature load at the product and the heat generated by its own power consumption. For example, due to the failure of the heat dissipation system and the high-temperature heat flow leakage of the equipment, the temperature of the component will exceed the upper limit of the allowable temperature. The component is exposed to high temperature. Stress: Under the long-term stable working condition of the storage environment temperature, the product bears long-term temperature stress. The high temperature resistance limit capability of electronic products can be determined by stepping high temperature baking test, and the service life of electronic products under long-term temperature can be evaluated through steady-state life test (high temperature acceleration).
Changing temperature stress means that when electronic products are in a changing temperature state, due to the difference in the thermal expansion coefficients of the functional materials of the product, the material interface is subjected to a thermal stress caused by temperature changes. When the temperature changes drastically, the product may instantaneously burst and fail at the material interface. At this time, the product is subjected to temperature change overstress or temperature shock stress; when the temperature change is relatively slow, the effect of changing temperature stress is manifested for a long time The material interface continues to withstand the thermal stress generated by the temperature change, and micro-cracking damage may occur in some micro areas. This damage gradually accumulates, eventually leading to the product material interface cracking or breaking loss. At this time, the product is exposed to long-term temperature. Variable stress or temperature cycling stress. The changing temperature stress that electronic products endure comes from the temperature change of the environment where the product is located and its own switching state. For example, when moving from a warm indoor to a cold outdoor, under strong solar radiation, sudden rain or immersion in water, rapid temperature changes from the ground to high altitude of an aircraft, intermittent work in the cold environment, the rising sun and back sun in space In the case of changes, reflow soldering and rework of microcircuit modules, the product is subjected to temperature shock stress; the equipment is caused by periodic changes in natural climate temperature, intermittent working conditions, changes in the operating temperature of the equipment system itself, and changes in communication equipment call volume. In the case of fluctuations in power consumption, the product is subjected to temperature cycling stress. The thermal shock test can be used to evaluate the resistance of electronic products when subjected to drastic changes in temperature, and the temperature cycle test can be used to evaluate the adaptability of electronic products to work for a long time under alternating high and low temperature conditions.
2. Mechanical stress
The mechanical stress of electronic products includes three kinds of stress: mechanical vibration, mechanical shock, and constant acceleration (centrifugal force).
Mechanical vibration stress refers to a kind of mechanical stress generated by electronic products reciprocating around a certain equilibrium position under the action of environmental external forces. Mechanical vibration is classified into free vibration, forced vibration, and self-excited vibration according to its causes; according to the movement law of mechanical vibration, there are sinusoidal vibration and random vibration. These two forms of vibration have different destructive forces on the product, while the latter is destructive. Larger, so most of the vibration test assessment adopts random vibration test. The impact of mechanical vibration on electronic products includes product deformation, bending, cracks, fractures, etc. caused by vibration. Electronic products under long-term vibration stress will cause structural interface materials to crack due to fatigue and mechanical fatigue failure; if it occurs Resonance leads to over-stress cracking failure, causing instant structural damage to electronic products. The mechanical vibration stress of electronic products comes from the mechanical load of the working environment, such as the rotation, pulsation, oscillation and other environmental mechanical loads of aircraft, vehicles, ships, aerial vehicles and ground mechanical structures, especially when the product is transported in a non-working state And as a vehicle-mounted or airborne component in operation under working conditions, it is inevitable to withstand mechanical vibration stress. Mechanical vibration test (especially random vibration test) can be used to evaluate the adaptability of electronic products to repetitive mechanical vibration during operation.
Mechanical shock stress refers to a kind of mechanical stress caused by a single direct interaction between an electronic product and another object (or component) under the action of external environmental forces, resulting in a sudden change in force, displacement, speed or acceleration of the product at an instant Under the action of mechanical impact stress, the product can release and transfer considerable energy in a very short time, causing serious damage to the product, such as causing electronic product malfunction, instant open/short circuit, and cracking and fracture of the assembled package structure, etc. . Different from the cumulative damage caused by the long-term action of vibration, the damage of mechanical shock to the product is manifested as the concentrated release of energy. The magnitude of the mechanical shock test is larger and the shock pulse duration is shorter. The peak value that causes product damage is the main pulse. The duration of is only a few milliseconds to tens of milliseconds, and the vibration after the main pulse decays quickly. The magnitude of this mechanical shock stress is determined by the peak acceleration and the duration of the shock pulse. The magnitude of the peak acceleration reflects the magnitude of the impact force applied to the product, and the impact of the duration of the shock pulse on the product is related to the natural frequency of the product. related. The mechanical shock stress that electronic products bear comes from the drastic changes in the mechanical state of electronic equipment and equipment, such as emergency braking and impact of vehicles, airdrops and drops of aircraft, artillery fire, chemical energy explosions, nuclear explosions, explosions, etc. Mechanical impact, sudden force or sudden movement caused by loading and unloading, transportation or field work will also make the product withstand mechanical impact. The mechanical shock test can be used to evaluate the adaptability of electronic products (such as circuit structures) to non-repetitive mechanical shocks during use and transportation.
Constant acceleration (centrifugal force) stress refers to a kind of centrifugal force generated by the continuous change of the direction of movement of the carrier when electronic products are working on a moving carrier. Centrifugal force is a virtual inertial force, which keeps the rotating object away from the center of rotation. The centrifugal force and the centripetal force are equal in magnitude and opposite in direction. Once the centripetal force formed by the resultant external force and directed to the center of the circle disappears, the rotating object will no longer rotate Instead, it flies out along the tangential direction of the rotation track at this moment, and the product is damaged at this moment. The size of the centrifugal force is related to the mass, movement speed and acceleration (radius of rotation) of the moving object. For electronic components that are not welded firmly, the phenomenon of components flying away due to the separation of the solder joints will occur under the action of the centrifugal force. The product has failed. The centrifugal force that electronic products bear comes from the continuously changing operating conditions of electronic equipment and equipment in the direction of movement, such as running vehicles, airplanes, rockets, and changing directions, so that electronic equipment and internal components have to withstand centrifugal force other than gravity. The acting time ranges from a few seconds to a few minutes. Taking a rocket as an example, once the direction change is completed, the centrifugal force disappears, and the centrifugal force changes again and acts again, which may form a long-term continuous centrifugal force. Constant acceleration test (centrifugal test) can be used to evaluate the robustness of the welding structure of electronic products, especially large-volume surface mount components.
3. Moisture stress
Moisture stress refers to the moisture stress that electronic products endure when working in an atmospheric environment with a certain humidity. Electronic products are very sensitive to humidity. Once the relative humidity of the environment exceeds 30%RH, the metal materials of the product may be corroded, and the electrical performance parameters may drift or be poor. For example, under long-term high-humidity conditions, the insulation performance of insulating materials decreases after moisture absorption, causing short circuits or high-voltage electric shocks; contact electronic components, such as plugs, sockets, etc., are prone to corrosion when moisture is attached to the surface, resulting in oxide film , Which increases the resistance of the contact device, which will cause the circuit to be blocked in severe cases; in a severely humid environment, fog or water vapor will cause sparks when the relay contacts are activated and can no longer operate; semiconductor chips are more sensitive to water vapor, once the chip surface water vapor In order to prevent electronic components from being corroded by water vapor, encapsulation or hermetic packaging technology is adopted to isolate the components from the outside atmosphere and pollution. The moisture stress that electronic products bear comes from the moisture on the surface of the attached materials in the working environment of electronic equipment and equipment and the moisture that penetrates into the components. The size of the moisture stress is related to the level of environmental humidity. The southeast coastal areas of my country are areas with high humidity, especially in the spring and summer, when the relative humidity reaches above 90% RH, the influence of humidity is an unavoidable problem. The adaptability of electronic products for use or storage under high humidity conditions can be evaluated through steady-state damp heat test and humidity resistance test.
4. Salt spray stress
Salt spray stress refers to the salt spray stress on the surface of the material when electronic products work in an atmospheric dispersion environment composed of salt-containing tiny droplets. Salt fog generally comes from the marine climate environment and the inland salt lake climate environment. Its main components are NaCl and water vapor. The existence of Na+ and Cl- ions is the root cause of corrosion of metal materials. When the salt spray adheres to the surface of the insulator, it will reduce its surface resistance, and after the insulator absorbs the salt solution, its volume resistance will decrease by 4 orders of magnitude; when the salt spray adheres to the surface of the moving mechanical parts, it will increase due to the generation of corrosives. If the friction coefficient is increased, the moving parts may even become stuck; although encapsulation and air-sealing technology are adopted to avoid the corrosion of semiconductor chips, the external pins of electronic devices will inevitably often lose their function due to salt spray corrosion; Corrosion on the PCB can short-circuit adjacent wiring. The salt spray stress that electronic products bear comes from the salt spray in the atmosphere. In coastal areas, ships, and ships, the atmosphere contains a lot of salt, which has a serious impact on the packaging of electronic components. The salt spray test can be used to accelerate the corrosion of the electronic package to evaluate the adaptability of the salt spray resistance.
5. Electromagnetic stress
Electromagnetic stress refers to the electromagnetic stress that an electronic product bears in the electromagnetic field of alternating electric and magnetic fields. Electromagnetic field includes two aspects: electric field and magnetic field, and its characteristics are represented by electric field strength E (or electric displacement D) and magnetic flux density B (or magnetic field strength H) respectively. In the electromagnetic field, the electric field and the magnetic field are closely related. The time-varying electric field will cause the magnetic field, and the time-varying magnetic field will cause the electric field. The mutual excitation of the electric field and the magnetic field causes the movement of the electromagnetic field to form an electromagnetic wave. Electromagnetic waves can propagate by themselves in vacuum or matter. Electric and magnetic fields oscillate in phase and are perpendicular to each other. They move in the form of waves in space. The moving electric field, magnetic field, and propagation direction are perpendicular to each other. The propagation speed of electromagnetic waves in vacuum is the speed of light ( 3×10 ^8m/s). Generally, the electromagnetic waves concerned by electromagnetic interference are radio waves and microwaves. The higher the frequency of electromagnetic waves, the greater the electromagnetic radiation ability. For electronic component products, electromagnetic interference (EMI) of the electromagnetic field is the main factor affecting the electromagnetic compatibility (EMC) of the component. This electromagnetic interference source comes from the mutual interference between the internal components of the electronic component and the interference of external electronic equipment. It may have a serious impact on the performance and functions of electronic components. For example, if the internal magnetic components of a DC/DC power module cause electromagnetic interference to electronic devices, it will directly affect the output ripple voltage parameters; the impact of radio frequency radiation on electronic products will directly enter the internal circuit through the product shell, or be converted into Conduct harassment and enter the product. The anti-electromagnetic interference ability of electronic components can be evaluated through electromagnetic compatibility test and electromagnetic field near-field scanning detection.
Post time: Sep-11-2023